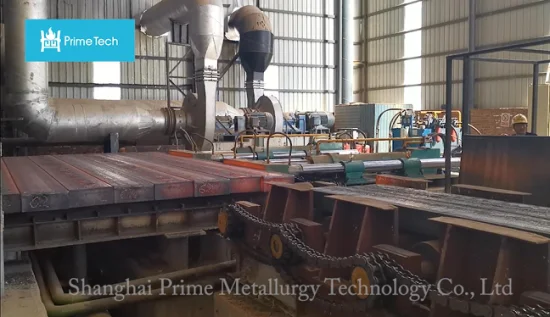
Coal Industrial Purification System Gas Station Gasifier Chinese Supplier
Basic Info
Model NO. | Pusher Type Furnace |
Condition | New |
Power Source | Gas, Hydraulic, Pneumatic |
Automatic Grade | Automatic |
Type | Steel Rolling Equipment |
Certification | ISO, CE |
Low Consumption | Save Energy, Regenerativ Combustion, Heat Recovery |
Uniform Temperature | Small Temperature Difference of Blank Section |
Scale Loss | Low. Air-Fuel Ratio Adjustment, Reducing Atmospher |
Nox Emission | Low Nox Combustion, Low Nox Burners |
Transport Package | Frame Packaging/Woodencase Packaging |
Specification | Customized |
Trademark | PRIME |
Origin | China |
HS Code | 8417100000 |
Production Capacity | 20sets/Year |
Packaging & Delivery
Package size per unit product 3000.00cm * 1000.00cm * 500.00cm Gross weight per unit product 1300000.000kgProduct Description
1. General design principle and technical solutions
The application of reheating furnace meets the production requirements of high production, high quality, low consumption, pollution-free and production automation.The technical solutions for the design of reheating furnace and its main auxiliary electric & instrument control system ensure reliable production, advanced indexes, and practical technology.
1.1Technical solution for heating capability
• The theoretical combustion temperature of the fuel is one of the main factors affecting the heating capacity of the furnace. High theoretical combustion temperature of high calorific fuel, high furnace temperature coefficient and high furnace hearth temperature reachable may enhance the heating effect and increase the heating capability of a furnace by increasing the temperature of the furnace hearth. Considering that the project is mainly applied for alloy steel heating, a longer preheating section is required to meet the requirement for low charging temperature and slow temperature rise of alloy steel and thus the strength of the furnace bottom steel is properly taken as a low-value, in which case the effective length of the heating furnace is designed as 24m and bottom strength 347kg/m2·h at the rated output.• A certain potential shall be considered for the design of heating furnace to meet the heating requirements when rolling the materials of different specifications. In this proposal, the heating load is designed according to maximum cold charging output of 50t/h, and on this basis, 15% extra coefficient is reserved for the burner, leaving adequate capability for increase in production in the future.• Extra capability of 20% is considered for the design and selection of fans.• The application of air preheater will preheat combustion air up to ~500°C, which increases the theoretical combustion temperature and helps to increase production.• The reliable and well-developed automation system ensures the perfectness ratio of combustion system
1.2 Solution for control of oxidation loss
The formation process of scale mainly depends on the furnace atmosphere, furnace temperature and the retention time of billets at high temperature• Enhancing the burning and mixing of air and fuel is a fundamental measure and furnace atmosphere control is the main way to reduce oxidation loss. Excessive oxygen will promote the oxidation reaction. The operation is too close to the chemical equivalent reaction and will cause the generation of iron scale with stronger viscosity;• Reasonable distribution of heating load in each section of the heating furnace is the key to lower oxidation burning loss.• Start by optimizing the distribution of heating load and operating procedures and limit the residence time of the billet surface at a temperature higher than 900°C, that is, operate the furnace according to the output and target discharge temperature, and take strict measures of decreasing heating during the rolling stop;• Adjust the opening degree of the flue damper rationally for good control of furnace pressure.• Heating temperature under the heating furnace should not be too low, and it is required to leave enough space for the accumulation of scale.
1.3 Deslagging solution of pusher-type reheating furnace
The deslagging cycle of heating furnaces is generally 3 to 4 months in China. A furnace is required to shut down for about 1 week for each deslagging, which will cause the suspension of production, the increase of workers' labor intensity, and to some extent influence the service life of the furnace due to frequent start-stop of the heating furnace.Currently, the deslagging solutions of pusher-type reheating furnaces against the design of the furnace body and its ancillary types of equipment in China are as follows:• The furnace body is provided with a necessary access door to facilitate the troubleshooting of the furnace and the transportation of furnace slag.• The side wall in the soaking section is equipped with a necessary manual slag door to facilitate the removal of part of the slag with a shovel without shutting down the furnace.• Shut down the furnace and clean up the furnace slag manually after the furnace has been operating for a certain period of time.
1.4 Technical solution to improve the heating quality
In consideration of the requirements of temperature homogeneity of the roller against billet section and length direction, that is, "low-temperature thorough burning", the heating mode/heating capacity/optimized operating system of the reheating furnace shall necessarily satisfy the requirement. The application of proper furnace type and burners will ensure the quick heating up of the furnace, temperature uniformity of heated billets and low oxidation loss. The improvement in heating quality will also reduce the rolling pressure, the energy consumption of the roller, and potential accidents to some extent.• The heating furnace is divided into a soaking section and a heating section, with good flexibility.• Since the lower part of the billets is shielded to a greater extent by the water pipe at the furnace bottom, the heating capacity should be appropriately increased beneath the furnace.• For temperature homogeneity along with the billet length direction are as follows: Selection of burner type layout of burners location of burners inside of furnace hearth Furnace hearth pressure control and emission • Temperature deviation between surface and center is as follows: Sufficient heat in the heating zone The reasonable heating time of the billet inside the furnace To determine the length of the soaking section for better soaking.
1.5 Energy saving measures
• The application of inserted tube-type metallic heat exchanger will preheat the air temperature up to ~500°C, which may have a significant energy-saving function.• Preheating section shall be reserved as long as possible under the condition that production output is guaranteed.• Low cement heavy-weight castable is applied for the overall pouring of the working face; a composite structure is applied for the furnace top/bottom/wall to minimize heat loss of the furnace body.• Optimize the furnace door and make the structural design for flexible opening and tight sealing to reduce the heat loss from furnace gas overflow and cold air intake.
After Sales Service
After Sales Service
One year guarantee (replacement or repairment for free)Three years regular return visits and resolve the technical problemesFive years free technical supportPatent Certificate
A kind of Direct Travel reversal valve for heat storage type combustion | AbstractThe utility model discloses a kind of Direct Travel reversal valve for heat storage type combustion, including the valve body, valve rod, power part, the first sealing structure and the second sealing structure. Wherein, the power part is removably disposed on the valve body, and its output end connects the valve rod and moves linearly for the driving stem. The valve inner is deep into the lower end of the valve rod, and the valve rod is connected by the first sealing structure with body movable sealing. The second sealing structure is set to the lower end of the valve rod, the open and close of the burner side interface for the application valve body. The application is sealed valve rod and valve body of the first sealing structure. It is sealed by the second sealing structure for the burner side interface. It has a better seal effect compared with the existing technology. In addition, the application is moved linearly using a cylinder as a dynamical element driving the second sealing structure, guaranteeing that the stroke of the second sealing structure is the shortest, therefore the used time is minimized, thus the working sensitivity and working efficiency is improved. | |
A kind of sealing mechanism for valve | AbstractThe utility model discloses a kind of sealing mechanism for the valve, which is arranged on the valve body and the valve rod, including the sealing valve plate, the first sealing ring, the position limiting sealed part and the pedestal. A pedestal is fixed on the valve body, and the position limiting sealed part and the first sealing ring is installed in the sealing valve plate, and the valve rod drives the sealing valve plate so that the valve rod and valve body are in sealed or open state. Under the sealing state, the position limiting the sealed part, the first sealing ring, and the sealing valve plate form the first sealing, the second sealing and three seals with pedestal respectively. The application enhances the tightness of import or export by three seals, to solve the problems, such as dielectric leakage in the valve. | |
A kind of detachable burner connection structure | AbstractThe utility model discloses a kind of detachable burner connection structures, including a burner body, burner block heating furnace, transition piece, and compression connector. Wherein, the burner block is embedded in the furnace wall of the heating furnace, and the burner body and burner block flanged joint, the transition piece is fixed on the furnace wall, one end for compressing connector is detachably connected with the transition piece, and the flange connections of burner body and burner block are pressed on furnace wall by the other end. Firstly, can remove when the failure or burner is replaced and the compress connector and flange, heat-accumulating burner, and burner block are directly replaced, removing the furnace skin and furnace wall, and the operation such as furnace wall casting again without carrying out. Secondly, the present application addresses between burner body and burner block, and the problem of being caused by the gas leakage generated by the gap between the burner block and the furnace wall and sparkle. | |
A kind of burner connection structure | AbstractThe utility model discloses a kind of burner connection structures, including burner body, burner block, and heating furnace, wherein the burner block is embedded in the furnace wall of the heating furnace, and forms the first sealing and the second sealing with the furnace wall; Burner body is detachable with burner block and furnace wall respectively, and the third sealing and the 4th sealing are formed between burner body and burner block. The application improves the tightness of the burner, avoids generating gaps in the use process, and prevents the mixed gas in the heating furnace from escaping by the way that two seals are respectively arranged between the burner block and the furnace wall, between the burner block and the burner body. | |
A kind of blending system based on heat storage type combustion | AbstractThe blending system based on heat storage type combustion that the utility model relates to a kind of, set on the empty cigarette module or/and coal smoke module of the regenerative combustion system, by extracting flue gas from the flue gas general pipeline of the regenerative combustion system and the heating furnace is blown into from reversal valve to making in the heating furnace into oxygen deprivation state, the formation for inhibiting furnace high-temperature area, to reduce the number of nitrogen oxides in the flue gas. Meanwhile, the application can be entered air existing for public domain or coal gas blowback in the heating furnace by the flue gas of pump back, not only saving resource, but also reducing the content of coal gas and air in flue gas general pipeline, to further improve the safety coefficient of the system. | |
A kind of blowback system based on heat storage type combustion | AbstractThe utility model relates to a kind of blowback system based on heat storage type combustion, including blowback main pipe rail, blowback branch, and air extractor, wherein the air extractor is arranged on the blowback main pipe rail, blowback main pipe rail is connected to the flue gas general pipeline of coal smoke module in the regenerative combustion system, one end of blowback branch is connected to blowback main pipe rail, and the other end is connected to the end of the common conduit. Stop the air inlet, before the smoke evacuation stage in the air inlet side of the heating furnace, the utility model enters the coal gas blowback in the common conduit in the coal smoke module in the heating furnace, to solve the smoke evacuation side of the heating furnace and when air inlet side is converted, the coal gas in regenerative combustion system at common conduit is discharged with flue gas and the wasting of resources, environmental pollution and the safety issue that generate. | |
A kind of burner connection structure based on heat storage type combustion | AbstractThe burner connection structure is based on heat storage type combustion that the utility model discloses a kind of is related to the installing area of the burner body in the regenerative combustion system. The burner connection structure includes the heating furnace and the burner body on the heating furnace. Wherein, the multithread stock spout of the connection burner body is preset on the furnace wall of the heating furnace; the burner body is detachably connected with the furnace wall, and the contact surface archwise sealing of the two. The application fundamentally evaded because of factors such as physical change, the displacements of refractory material itself of furnace wall caused by the heating furnace in mixed gas evolution and heating furnace the technical issues of burning with anger, and there is more preferably sealing effect and easy-to-dismount advantage compared with the existing technology. | |
It is a kind of segmentation, two-sided control regenerative combustion system | AbstractThe utility model discloses a kind of regenerative combustion system for dividing side, Discrete control, the regenerative combustion system singly preheated preheats empty soot system, and the regenerative combustion system of double preheatings preheats empty soot system and coal smoke subsystem.The subsystem preheated includes three-way diverter valve, air/gas general pipeline and sky cigarette/coal smoke general pipeline.Wherein, the two sides of each section of heating furnace are symmetrical arranged there are two three-way diverter valve, the burner interface of the burner of section side where three-way diverter valve includes the air/gas interface for connecting air/gas general pipeline, connects empty cigarette/coal smoke interface of sky cigarette/coal smoke general pipeline and connect it.The application divides side, Discrete control by air inlet to regenerative combustion system and smoke evacuation, it solves the problems, such as because of in-furnace temperature and pressure oscillation caused by frequently commutating, and loss caused by gas piping cross-infection and endanger, while have many advantages, such as that layout is simple again, be easy to construct, hardware cost is low, convenient for controlling. |
Company Profile
Company Profile
VisionWith decades of rapid development and accumulation, China has been perfect and mature on technology and management in various industrial areas, shaping a complete processing manufacturing industry with competitive price, well known for its excellent skill, high efficiency and hardworking team with qualification for personnel dispatching.At the time of economic globalization, it is our consistent target and objective to integrate and export all kinds of technology, management mode, engineering project and manpower as per the actual requirement of our client With our own abundant technical strength, superior integration capability of technology and resources, well experienced of project implementation and management as basis and platform;Let China go out to the world, and make the world know of China; ProfessionalProfessional technical and management team with abundant experience in the implementation of domestic and international projects;ResponsiveResponsively and meticulously, translating your needs into complete solutions;IntegrationIntegrating various technologies and resources in China and fulfilling complementary advantages, by relying on professional teams;MotivationMotivated to provide the optimal solution and quality products;ExceptionalExceptional, delivery and,implementation of projects to meet, your expectations;Our teamProfessional technical teamPrime is staffed with professional import & export team skilled with the practice of import and export business, including sea freight packing, logistics organization, L/C review, cargo booking, and customs clearance, L/C negotiation, double authentication of shipment documents, etc.All above personnel are well experienced in the execution of projects in Southeast Asia and Middle East. Complete procurement mechanismOur professional team of procurement offers strict management of supplier 's qualification inspection and selection, complete system of supplier listing, rating and elimination, to ensure the supplier is qualified and capable of implementing the project and supplied with product of high quality, and maintain a healthy and good condition of credibility, contract settlement and capital flow management.Quality management systemOur complete quality management system , the process control covering from Scheme formulation , engineering technology, detailed design, to processing and manufacturing of equipment and material , ex-factory test and site erection and commissioning till it put into production, which through multi-level inspection, tour inspection, supervision and node control can ensure quality of the final product.Well experiencedExecutive team is abundant in experience of overseas project implementation with similar project working experiences, esp. experience in Southeast Asia, Middle East projects;
ISO System Certification
Partners